サプライチェーンにおけるキット化および組立のためのロボットシステム
キット化と組立におけるロボット自動化の利点
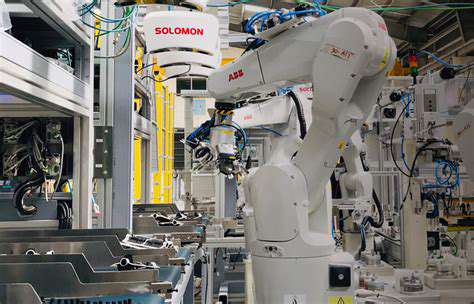
効率性と生産性の向上
ロボット自動化システムは、手順を合理化するために設計されています。
キット化と組立のためのロボットシステムの種類
キット化のための協働ロボット (Cobot)
協働ロボット (Cobot) は、人間労働者と安全かつ効果的に相互作用するように設計されています。キット化アプリケーションでは、Cobot は、ビン、トレイ、またはその他の場所から部品を拾うような反復的な作業に優れています。
THE END
More about サプライチェーンにおけるキット化および組立のためのロボットシステム